Concrete is the most widely used manufactured material on earth. Each year, 32 billion tonnes of concrete are produced, delivering 2.9bn tonnes of associated carbon dioxide emissions.
It accounts for 7 percent of global CO₂ emissions. To put that into perspective, if concrete were measured as a country, it would be the world’s third-biggest CO₂ polluter, just behind China and the US.
Fortunately, startups are leading the construction industry to a low-carbon future. Here's some companies to have on your radar:
Carbonaide (Finland)
When industrial side streams are used in the mix instead of normal cement, the result is concrete with a negative carbon footprint.
Among the possible side streams are steel industry slags, green liquor dregs, and bio-ash.
Carbonaide has developed an effective carbonation method, which allows the binding of carbon dioxide into concrete blocks using an automated system at atmospheric pressure.
Concrete manufactured with this method had a negative calculated carbon footprint of -60 kg per cubic metre of concrete — a huge saving to the carbon footprint of conventional concrete which is approximately 250–300 kg per cubic metre.
The method is compatible with the current concrete manufacturing processes and can, therefore, be used for manufacturing all precast concrete elements and products.
Concretene (UK)
Concretene uses nanomaterial technology to reduce the carbon footprint of the construction industry.
The company has created concretene, a graphene-enhanced admixture for concrete, engineered to enhance performance and sustainability.
The technology was originally developed by Nationwide Engineering Research & Development (NERD) and The University of Manchester’s Graphene Engineering Innovation Centre (GEIC).
Specifically, the technology incorporates graphene, an atomically thin form of carbon, which improves concrete microstructure, significantly increasing compressive, tensile and flexural strength, reducing curing periods, microcracking and permeability.
It’s suitable for use in existing batching plants, requiring no extra training or equipment, and can be scaled at a viable cost.
Nanogence (Switzerland)
Nanogence is pioneering carbon-avoidance technology through material science research. It develops eco-friendly smart catalyst technology for the construction and building industry by selectively enhancing the formation of interlocking crystals responsible for binding, thus improving the strength and durability of cementitious material (characteristic in cement). This saves up to 40 percent of carbon emissions without changing the current manufacturing process.
Nanogence’s technology either reduces cement demand or replaces it with eco-friendly materials while preserving the strength and performance of the concrete.
The technology can also be integrated at the cement production level without compromising product performance and, more importantly, without costly changes in the current process.
Biozeroc (Germany)
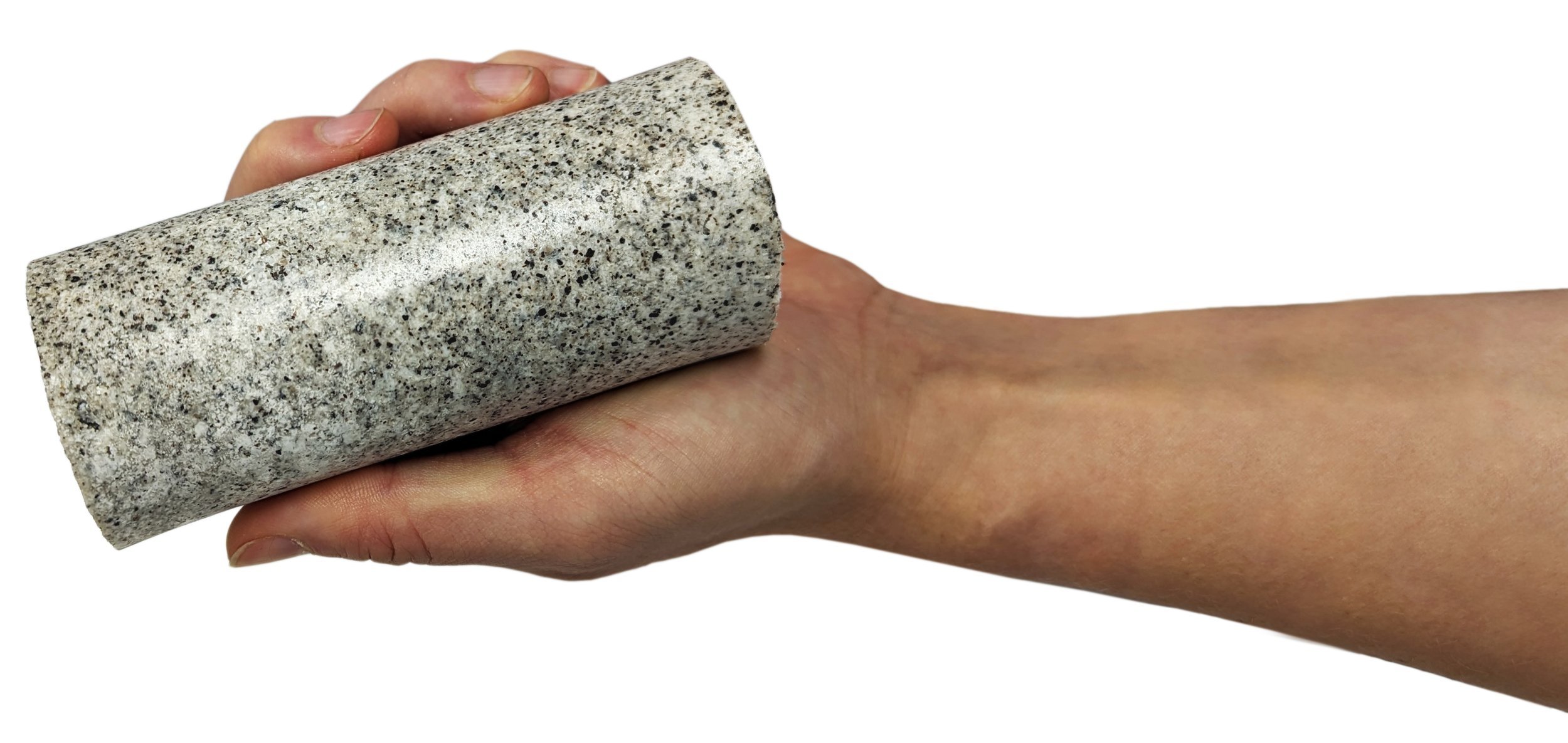
Biozeroc uses biotech, nanotech and chemical science to grow the carbon negative construction materials of the future. BioConcrete is a patent-pending solution that removes the need for cement in concrete manufacturing and enables high strength and flexibility.
Instead, it uses naturally occurring bacteria mixed with organic feedstocks and circular reagents.
Bio-concrete has previously been limited to making thin elements or healing cracks, which is where BioZeroc enters the picture.
BioZeroc is bridging the gap between biotech and smart scale-up technology to create elements of a larger size and higher commercial viability than what’s been achieved before.
Alcemy (Germany)
Many companies are working to reduce the carbon emissions of concrete.
However, according to Alcemy, it is difficult to produce reliable low-carbon concrete at scale. Further, it can be vulnerable to fluctuations in raw materials and operating conditions and thus difficult to produce with reliable quality. Adding to the challenge: the final quality of concrete can only be measured weeks AFTER it has been processed on the construction site — far too late to be corrected.
Alcemy’s software helps cement and concrete producers receive precise quality predictions during production. Based on these prediction models, its AI identifies which production parameters need to be adjusted to mitigate the impact of fluctuations. Thus, the quality of cement and concrete can be optimised before delivery — an industry first.
The result is significantly more consistent product quality, allowing producers to safely replace burnt limestone with lower cost low-carbon materials.
Cloud Cycle (UK)
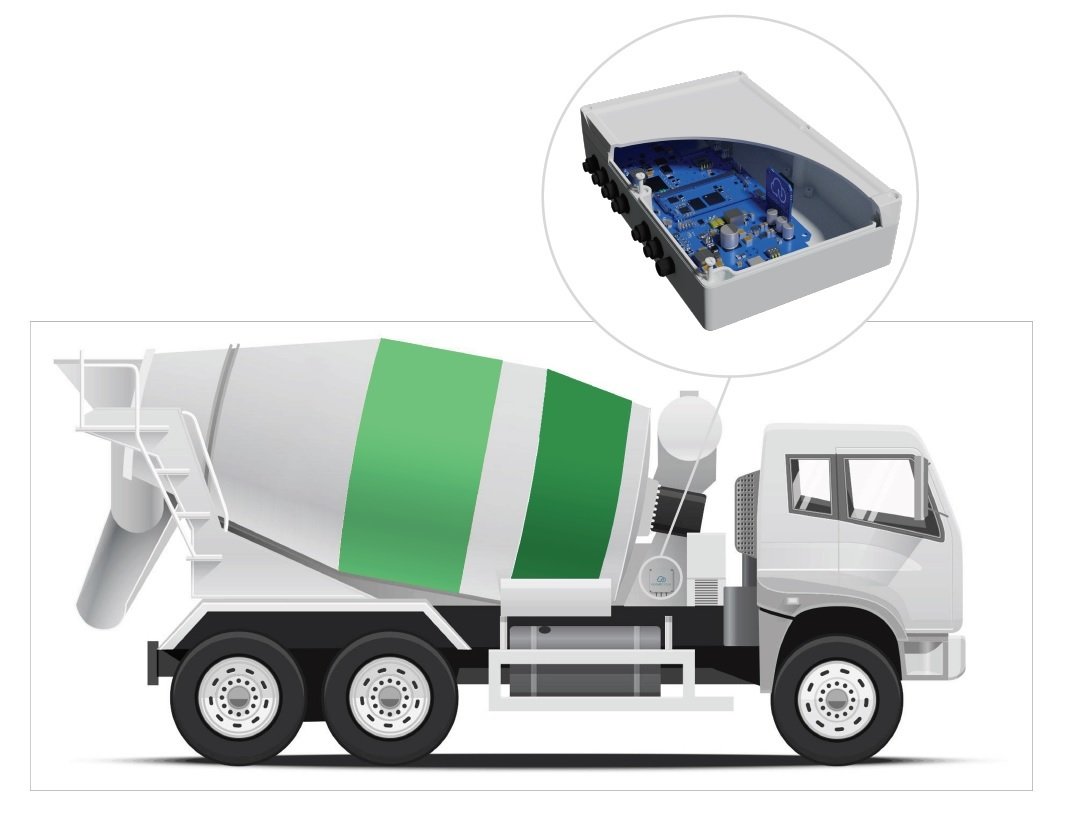
Data is knowledge and Cloud Cycle is digitising concrete.
During the concrete life cycle, concrete has a usable life of about 1.5 hours. Around 5 percent of all cement is wasted. However, in summer, it loses workability more rapidly, leading to rejection and waste. Cloud Cycle has developed a unique technology to help the entire concrete supply chain.
CloudCycle has developed an on-truck device and sensor array that collects data, enabling companies to track, monitor, and measure their digitised concrete.
A combination of machine learning on the edge and cloud analytics provides real-time and predictive analytics, which ensures concrete meets specifications and prevents waste. This provides transparency for operations, allowing concrete suppliers to assess the performance of batch plants, trucks, and job sites.
Silicate (Ireland)
Sidestream tech — giving a material another life through another use case is a hot topic in circular innovation. And it's not just in food tech. Dublin startup Silicate is turning surplus concrete into a low-cost, carbon removal tool via a process called 'enhanced weathering' — and it is an industry-first.
Silicate grounds surplus concrete into fine dust and gives it to farmers to spread onto their fields. Concrete can improve crop productivity by optimising soil pH, enhancing plants' natural resistance to herbivory through the release of bioavailable silica, and it can provide vital nutrients to the soil.
Silicate then measures the level of CO2 removed from the atmosphere and sells carbon credits of that value to private companies like Klarna and Milkywire.
Lead image: Life of Pix.
Would you like to write the first comment?
Login to post comments