Industrial tech has matured significantly since the hype-driven era of the mid-2010s.
The challenges of hardware development are undeniable, yet the convergence of IoT, AI, robotics, and data science continues to yield meaningful solutions to longstanding industrial problems.
Here’s some of the early-stage companies leading the way:
FaradaIC Sensors (Germany)
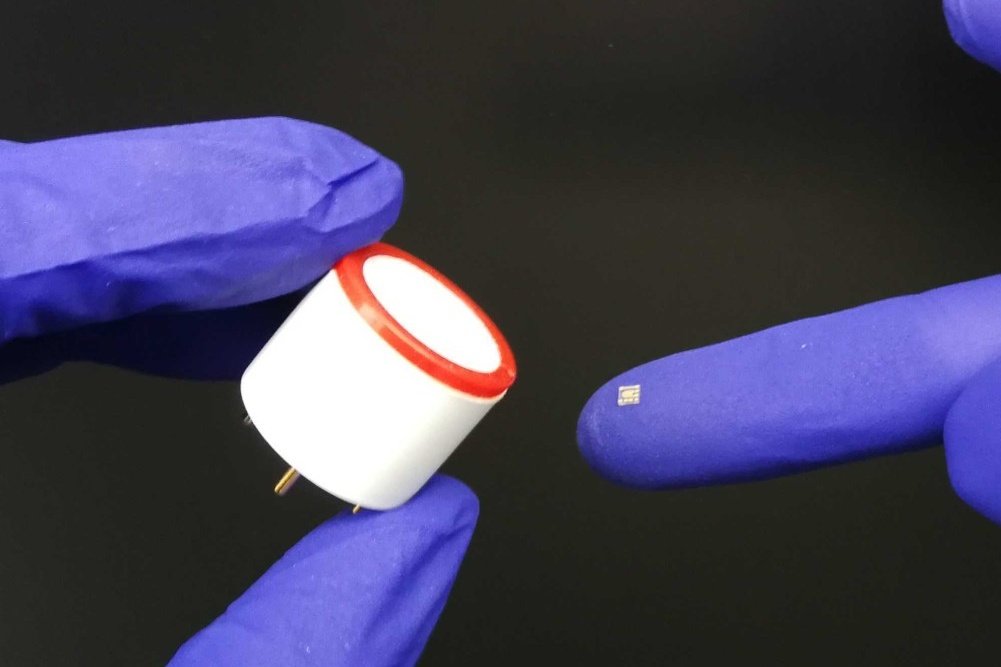
Currently, gas sensors are too bulky (several cm), too expensive (upwards of $400), and too power-hungry for many devices.
FaradaIC Sensors is a fabless semiconductor and chemistry company combined. It miniaturised electrochemical gas sensors on microchips using microfabrication techniques.
It offers device manufacturers in IoT and consumer electronics a multigas sensing platform that combines miniaturisation, low power, and low cost, making it suitable for high-volume demands.
The company has raised €2.5 million.
Qlayers (The Netherlands)
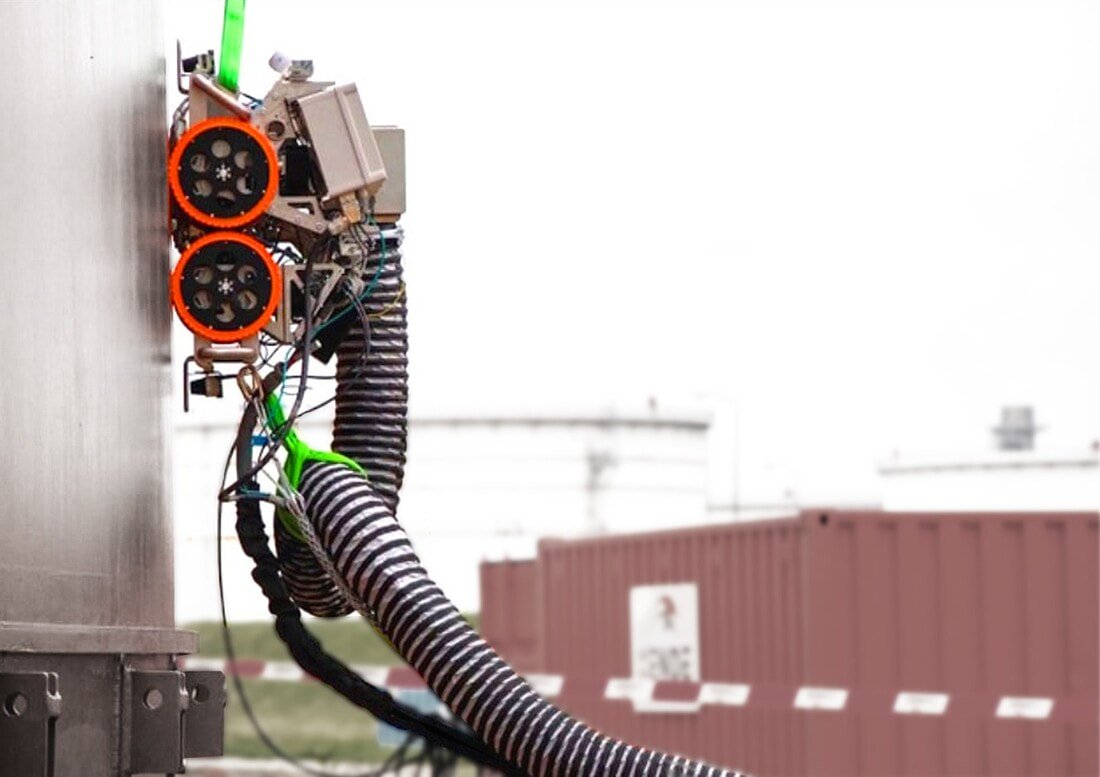
Qlayers has developed an automated robotic coating application to overcome the limitations of manual coating of large industrial surfaces like storage tanks and wind turbines by creating an environmentally friendly, safe, and reliable coating application process.
Its technology enables coating companies to deliver better and faster work onsite while keeping their personnel safe.
It can further create nature-based microstructures such as the drag-reducing ‘sharkskin’ microstructure in certified coatings at high speed to increase energy efficiency.´
The company has raised €371,400.
Touch Sensity (France)
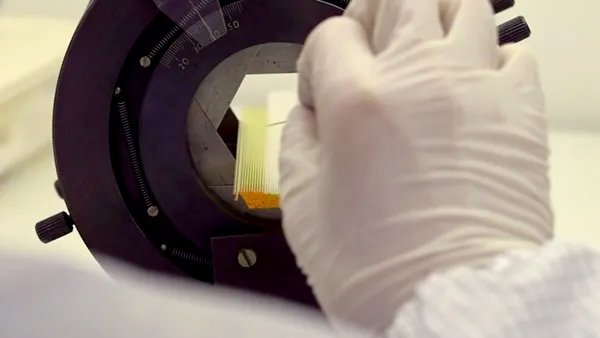
Touch Sensity develops technology known as Sensity Tech, enabling materials to be sensitive to physical interactions without the need for traditional sensors.
In Sensity Tech, the entire surface, whether solid, flexible or even liquid, is used as the measuring instrument. Coupled with AI, the system locates and models in real-time all the physical interactions carried out on the material to analyse real-time data related to pressure, deformation, and other mechanical interactions, effectively transforming the material itself into a sensing instrument.
The potential applications of Touch Tech include aeronautics, the space industry, transportation, and maintenance.
The company has raised €3.1 million.
SYGLASS (Poland)
The custom photonics market faces long lead times, high costs, and skilled labour requirements, hindering efficiency and scalability.
SYGLASS has developed automated manufacturing of gradient optics elements, enabling rapid and scalable production of custom photonics.
This technology reduces lead times from over 10 weeks to a few days, eliminates the need for multiple machines and skilled personnel, and lowers production costs.
Specifically, SYGLASS uses AI and IoT to automate the production of custom optical elements, ensuring high repeatability and quality. Its system designs, tests, and customises nanostructured photonics quickly, setting a new industry standard for efficiency and scalability.
ADAXIS (France)
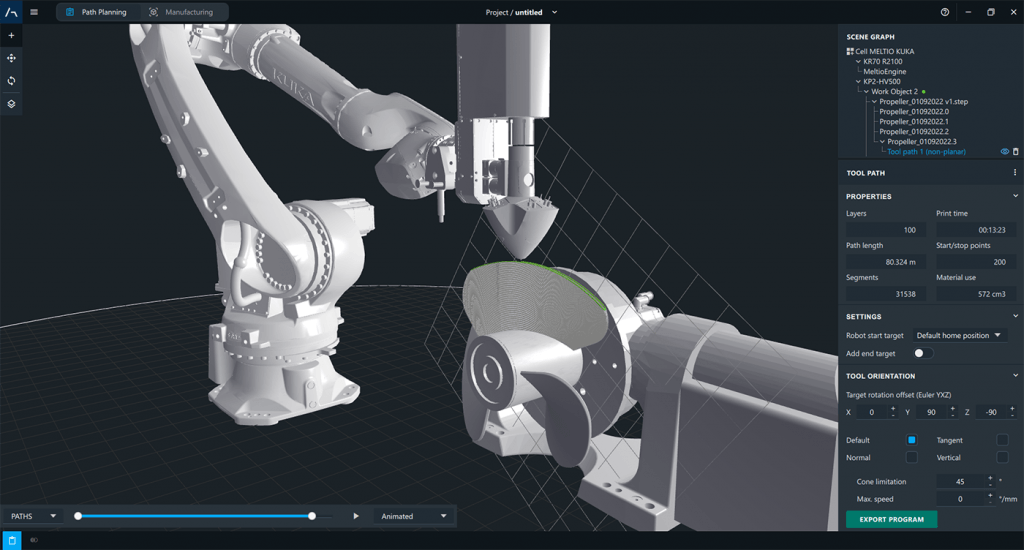
Image: ADAXIS.
While 3D printing microfactories have attracted interest in industrial sectors, mass adoption is in part hindered by the small size of the printable parts and the difficulty of programming the machines quickly and easily.
ADAXIS has developed software called AdaOne that turns any robotic arm into a flexible, high-volume 3D printer for metals, polymers, composites and concrete.
The power of the industrial robot makes it possible to produce very large parts with very complex shapes. Thanks to this technology, a motorboat over 4-metres long was printed in one go.
AdaOne covers all the tasks required to manufacture a part, from creating the program to supervising the process in real-time, including a multi-physics digital simulation.
The company has raised €1 million.
Covision Quality (Italy)
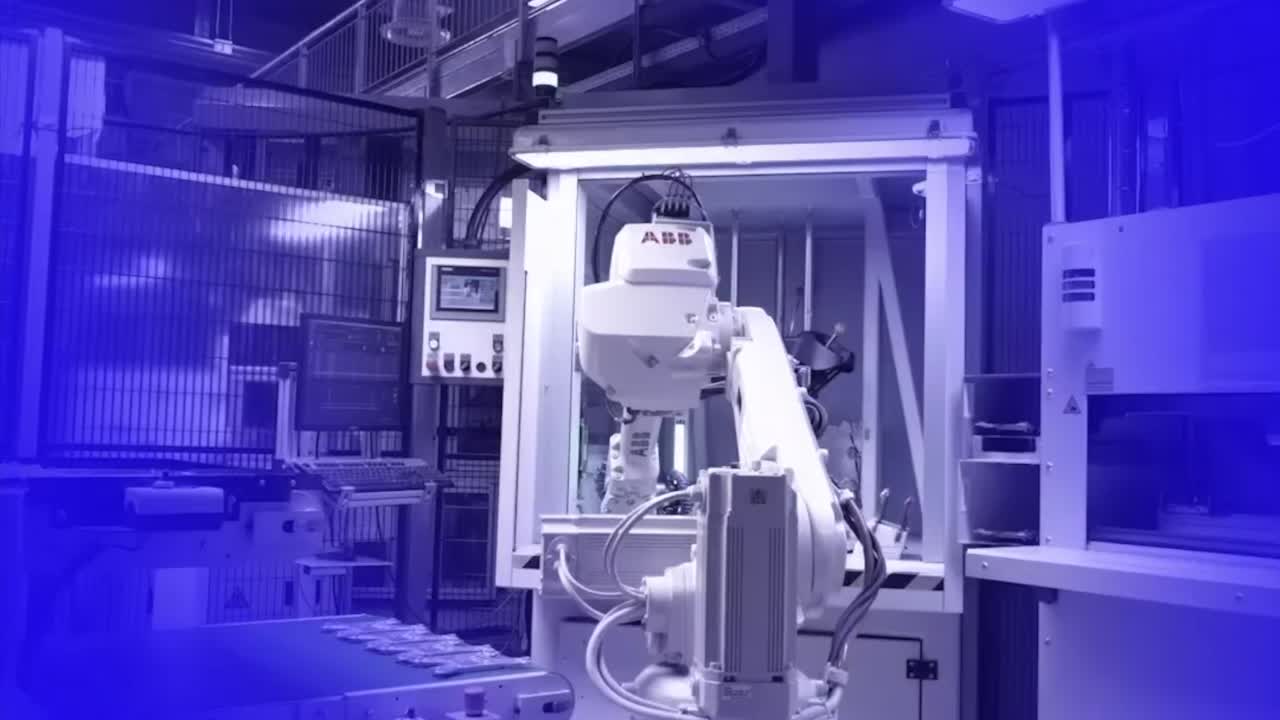
Covision Quality (Covision Lab) provides visual inspection software that uses unsupervised machine learning technology for industrial applications.
The technology can automate the end-of-line quality control process in various downstream industries that leverage non-ferrous metals such as aluminium, copper, and zinc as well as ferrous materials such as steel: construction, automotive, mechanical and electrical engineering, aerospace, and medical devices.
The software significantly reduces deployment time for visual inspection systems and decreases pseudo-scrap rates in manufacturing processes.
Would you like to write the first comment?
Login to post comments