When you think about the metaverse, your first thought is probably gaming, but technologies like AI, 3D imagery, and data analytics profoundly impact the rapid industrial transformation underway in the manufacturing, supply chain, and automotive sectors.
Today German startup RIIICO has raised $1.5 million in a pre-seed funding round led by Earlybird Venture Capital and US-based investors to push AI-driven digital twin creation forward. I spoke to co-founders CEO Felix Fink, and Jan Büchsenschütz, COO, to find out more.
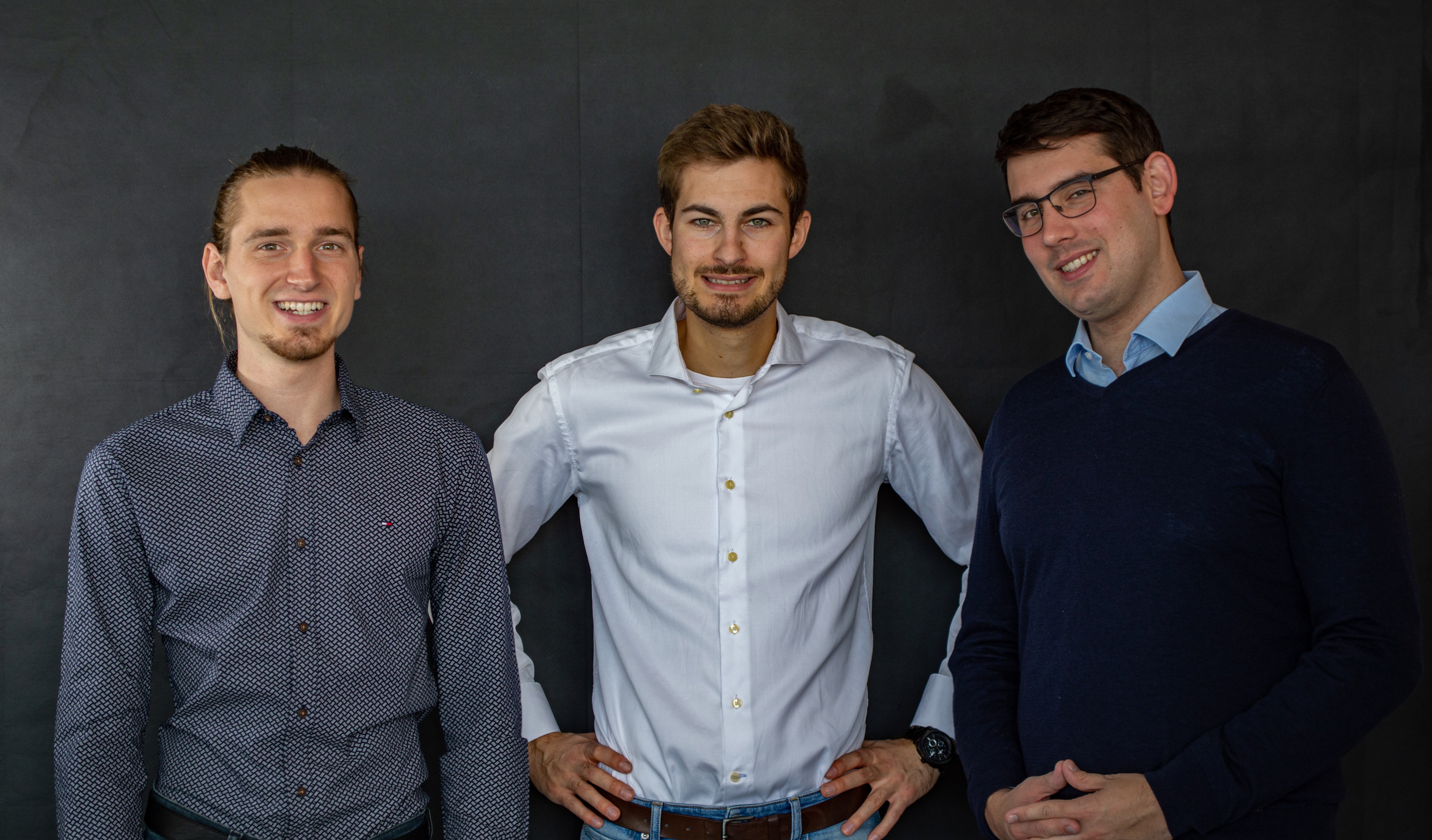
The challenge of digital transformation
Within manufacturing, the physical layout of the factory floor is rapidly changing as companies introduce new technology and machinery. Take the automotive industry, where the transition from diesel-powered to electric vehicles profoundly changes the process of industrial manufacturing.
But there are unique challenges in turning an automotive factory from the 1960s into an EV powerhouse. Creating a new factory layout in an operational facility is time-consuming and expensive.
A factory floor includes hundreds of pieces of equipment across various workstations. Moving industrial machinery is costly, not only in terms of the price of the devices but also the revenue lost while tools are down.
Introducing new lines, workstations, or layouts has a massive impact on the workflow and careful planning is necessary to avoid errors, minimise interruptions, and reduce delays.
RIIICO doesn't want to see established factories left behind, and according to Fink, "helping manufacturers to adapt towards the rapid change coming" as they work to stay competitive.
RIIICO empowers manufacturing companies to generate digital layouts at the digital factory floor level. The company utilises deep learning on 3D scans to retrieve insights directly from the shopfloor and translate those into a factory digital twin. Digital twin refers to a digital simulation or a virtual model of a product, process, service or functionality and can be used to visualise, monitor and represent a real factory in 3D.
RIIICO's advanced segmentation AI and meshing algorithms help manufacturers to translate their shopfloor reality directly into a transparent digital 3D model. The results are used across the factory software landscape for simulating the virtual start of production or different VR and AR applications.
Gaining traction from end-users is crucial
RIIICO enables faster design collaboration. Where it normally would be necessary to download a large software suite to a workstation, RIIICO can be used on a standard workplace laptop, speeding up the planning process and reducing the risk of errors. And it's made easy. Büchsenschütz explains:
"You can log in via a browser, you don't have to do prior training, and it's accessible."
This also has the advantage of involving end-users in the design process ."Many blue-collar workers have worked in their factory in Germany for 20 years. They are very loyal to the factory and want to contribute and have a lot of experience to share."
But change-making can be slow and is often met with resistance. Inside a factory, there is a myriad of hierarchies between the user and the decision-maker. But Büchsenschütz, shared:
"We got very lucky with the factory workers being our champions. We learnt that because we went through factory floors with engineers, and they said 'I could improve this, I could increase efficiency here, I could make a better space optimisation there.' And they felt our tool would give them a voice in the decision making."
Metaverse is going mainstream
Furthermore, collaboration in industrial transformation. Last year, Siemens' and NVIDIA's CEOs announced a groundbreaking plan to work together to build the Industrial Metaverse by connecting hardware and software from the edge to the cloud and leveraging the power of digital twins.
By now, most automotive players have heavily invested in this technology. 3D scans are currently generated worldwide using LiDAR scanners from, e.g. NavVis, FARO, and Hexagon Leica Geosystems. RIIICO is one of the first tools to automatically extract insights from this data.
RIIICO's existing customers include Siemens, Porsche, Volkswagen, Schaeffler and Schmitz Cargobull.
And using access control, companies can share the competitive advantages of digitisation. Historically, factory layouts and architecture are kept secret, but Fink explained, "nowadays the layout is not a secret anymore. The business advantage is in how fast they can adapt and implement new technologies. So they are willing to a certain degree, open it up to, for example, suppliers or other software vendors, partners who can gain value."
Fink notes:
"Startups bring this innovative disruption, where they say I'm just going to change the world. And I mean, you have to be a little bit crazy even to say you will do this. But combining this with corporates' decades of experience is very powerful.
Because in the end, you meet in the middle there, you can make a change that a corporation wouldn't have done in 10 years and a startup itself could have never done. There's enormous potential for this cooperation."
Would you like to write the first comment?
Login to post comments