We live in an era of fast fashion, where despite the best efforts of sustainability campaigners, people buy more clothes than they wear, resulting in them being burnt or ending up in landfills — according to EcoWatch, approximately 39.000 tons of unwanted garments are transported to the Atacama Desert annually, where they cover the dunes and cause significant environmental challenges.
Less than 1 per cent of used textiles worldwide are recycled into new textile fibres.
But now, a novel technology is changing things for the better.
German startup eeden has developed a chemical process that recovers cellulose from cotton and transforms polyester into its basic building blocks.
Both raw materials can then be processed into new, high-quality textile fibres and given a second life, creating a sustainable and economically beneficial closed loop.
I spoke to Steffen Gerlach, co-founder of eeden, to find out more.
eeden was founded in 2019 as a student project at the Hochschule Niederrhein, renowned throughout Germany for its textile department.
Usually, plants can only recover one fibre type from cotton-PET blends. eeden has managed to treat cotton and PET as effectively as possible so both components can be spun into fibres that retain a like-new quality.
The company plans to build a pilot plant in Q2 this year. Gerlach explained that the plant creates an opportunity to demonstrate its tech, closing the process loop and creating an ability to market pilots and deliver industrial-size product volumes to fibre producers.
Gerlach explained,
"Textile recycling is a complex puzzle. Different materials require specific processes, timed perfectly and in the right environment, to be separated without damage.
The goal is to recover valuable components while eliminating unwanted elements."
Further, technically feasible recycling requires both economic viability and environmental benefit.
Eeden is involved with the Circular Republic project, which offers a systemic perspective on transformation in the textiles industry with dedicated focuses on the various sections within textiles such as:
- Designing circular textiles.
- Categorising and separating textiles based on their composition, condition, and potential for reuse or recycling.
- retrieval of used textiles from consumers and other sources,
- mechanical recycling, chemical recycling, and upcycling.
"It brings together small demonstrators and pushes an exchange between different stakeholders to see how we can get from a linear textile industry to a circular economy.
Which actors must we bring in what order, and who has to deliver what?"
How do you incentivise a circular economy?
The EU Strategy for Sustainable and Circular Textiles aims to create a greener, more competitive sector more resistant to global shocks. The Commission's 2030 vision for textiles is that all textile products placed on the EU market are durable, repairable and recyclable, to a great extent made of recycled fibres, free of hazardous substances, produced in respect of social rights and the environment.
Gerlach asserts that different industry stakeholders have different perspectives.
"Some say the legislature is just an enabler; we're already ahead of that. Others are like, 'Let's see where regulations go and what we have to do.
Then, we'll decide what to do at that point, but maybe not more than that, and not earlier than regulations.'
It's also an opportunity for companies to create new business opportunities and competitive advantage. Changemakers are most critical to driving companies forward; they push for change within organisations and have enough clout to drive decision-making.
"It's about seeing potential, piloting an idea, testing, and seeing where it goes. Those are the actors we need to push innovation, not people waiting for regulations."
Eeden is currently working on its demonstration model with industrial washing companies. Large-scale items like bedsheets and tablecloths are rented or leased to industries like hotels and hospitals.
Gerlach explained;
"A good sized washing company washes about 30 to 50 tonnes of textiles daily, resulting in a few tonnes every month. They typically have to pay to dispose of the textiles once they are no longer repairable and become post-consumer waste."
But the company's eye is always on the goal of large-scale post-consumer waste, which is the most challenging "because everything could be in there in terms of materials and fibre proportions. It's not always on the label."
The company is also in discussion with the European chemical industry about possibilities for polyester by-products.
"It's a compelling storytelling opportunity in the journey of transforming plastic bottles into textiles and then back into chemicals. Highlighting this process can raise awareness about product life cycles, their impact on circularity and sustainability, and the challenge of greenwashing."
Recycled polyester is not without problems. Like virgin polyester, recycled versions shed tiny plastic fibres during washing, wearing, and production. These microplastics can contaminate our waterways and oceans, harming marine life.
Further, eventually, recycled polyester reaches its end of life and may end up in landfills, creating further environmental issues. Efforts by eeden to create new raw materials are critical to ensuring closed-loop polyester production.
eeden plans to launch a prototype textile made from their materials later this year, collaborating with textile collectors, fibre spinners, confectioners, and fashion brands to gather insights for the participants and the entire textile industry.
It's a great testament to the power of collaboration and shows the way forward for a closed loop textile manufacturing.
Other circular textile companies to watch
Petit Pli (UK) makes children's clothes that grow with your child.
Matr (Austria) creates a circular mattress economy for hotels with premium mattresses made from just steel and polyester.
Redivivum Technology (UK) is developing an AI-powered industry-first automated sorting solution for the fashion sector to enable better sorting of used garments from the post-consumer waste stream for reuse and recycling.
Seatrex (UK) has developed a groundbreaking method to convert byssus (mussel beard) waste into high-quality acoustic materials and products.
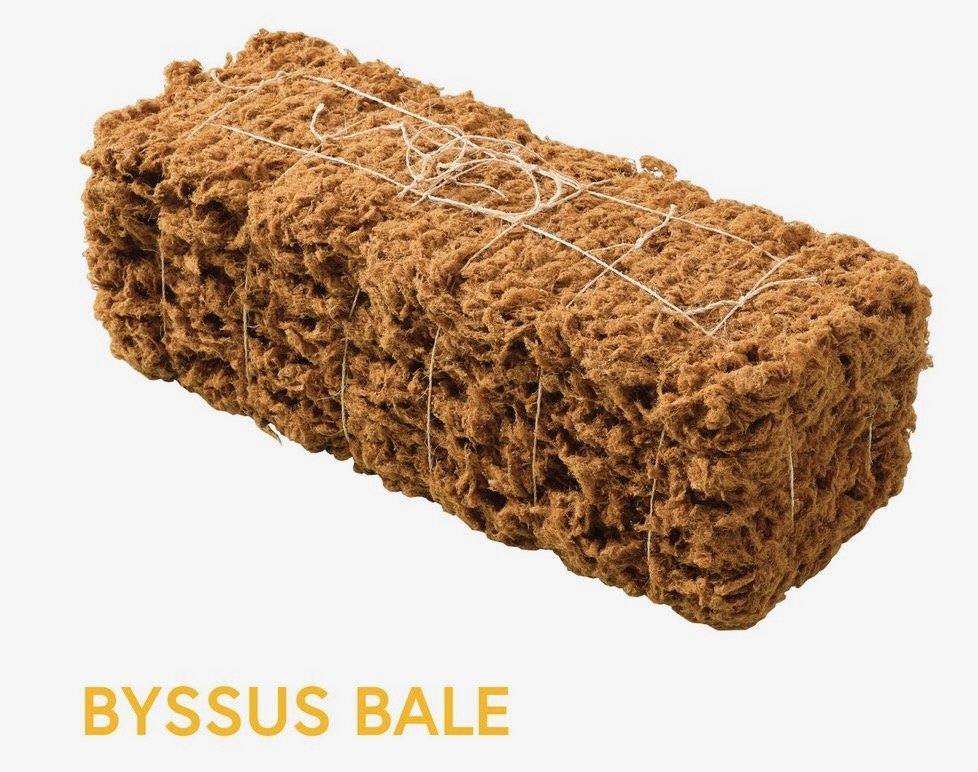
On (Switzerland) has developed Cyclon™, a program that allows consumers to rent running shoes. When worn out, the shoes are returned and recycled to create new shoe parts, promoting a more sustainable consumption model.
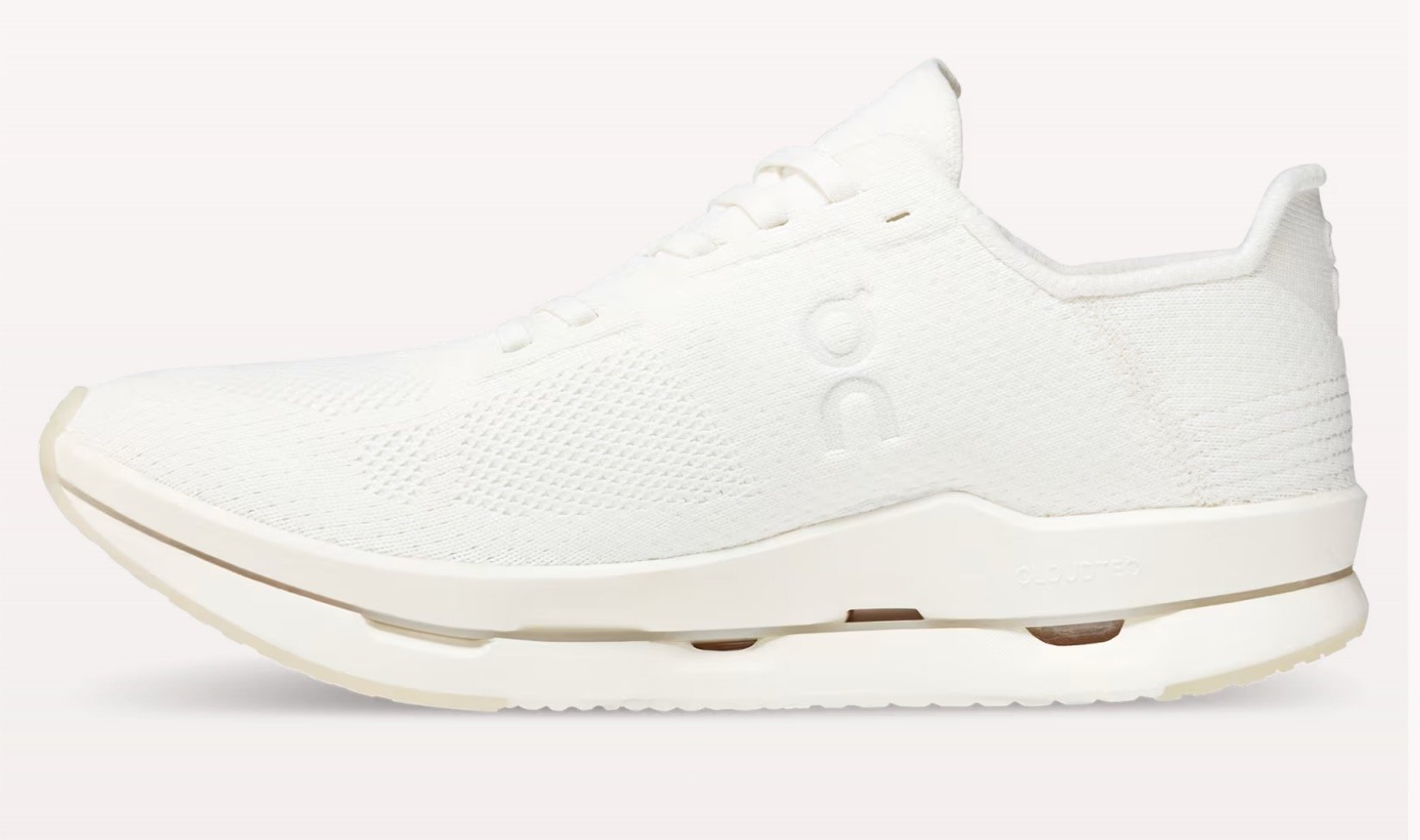
Lead image: Steffen Gerlach and Reiner Mantsch, co-founders of eeden. Photo: uncredited.
Would you like to write the first comment?
Login to post comments