Graphene is a two-dimensional material consisting of a single layer of carbon atoms arranged in a hexagonal lattice. It’s the thinnest material in the world and is known for its strength, electrical conductivity, and transparency.
Graphene was super hyped in 2010 — it's 200 times stronger than steel. It's 70 per cent more conductive than copper and has great barrier properties, making it suitable for a variety of applications.
The 2010 Nobel Prize in physics was even awarded to Andre Geim and Konstantin Novoselov for their experiments and discoveries related to graphene.
However, graphene failed to reach its potential due to production challenges, integration issues, cost, and the lack of research transitioning into real-world applications, such as industrial and commercial applications.
But a Swedish startup might have found a way forward.
Founded in 2017 by Dr. Mamoun Taher, Graphmatech is a Sweden-based material technology company that invents, develops, and supplies novel materials for sustainable industrial use.
Part of the problem with graphene is that flakes form clumps instead of dispersing evenly, and lose the miracle attributes. Graphmatech has pioneered the patented Aros Graphene, a unique hybrid material that addresses the common issue of graphene agglomeration, thereby enabling its large-scale industrial use.
The company has invented a clump-free powder — a ‘pinch of salt’ of cost-effective graphene, with smaller flakes and a couple of layers, which costs 1/20 of the price of what’s been traditionally on offer.
I spoke to company CEO Olivia Nestius, who shared that the company produces the fastest 3D printing material in the world. Its applications include conductive polymers, special plastics mixed with graphene to give them electrical properties.
Traditional conductive materials like metal are often heavy, expensive, or prone to corrosion. Graphmatech’s graphene-infused plastics offer a lighter, cheaper, and more durable alternative.
Further, normally, plastics don’t conduct electricity, but by adding graphene, Graphmatech can make them electrostatic dissipative (ESD) or even highly conductive, depending on the need. They conduct electricity in all directions – making them more reliable for high-tech applications.
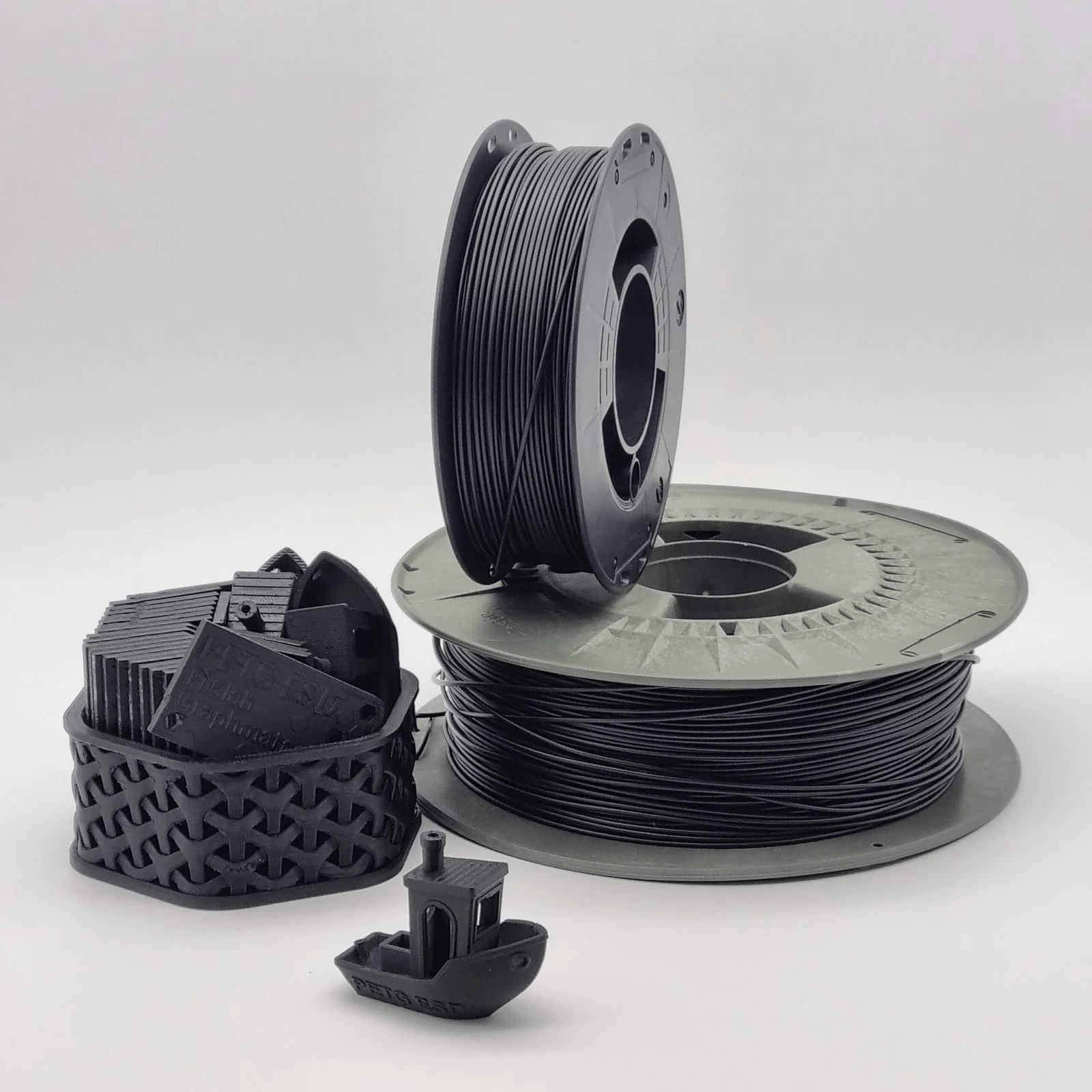
Potential applications include anti-static materials to prevent static electricity buildup that can damage electronics, car and aerospace parts for lightweight, strong, and conductive performance, 3D printing to create plastic components capable of carrying an electrical charge, and wearable tech.
According to Nestius:
“We have developed a set of patented technologies that makes it possible to work with several types of graphene and mix them to get the right type of properties that we want at a cost-efficient level.
Then we can apply this to large-scale industrial applications globally, making many different types of plastics and metals more high-performing and resource-efficient."
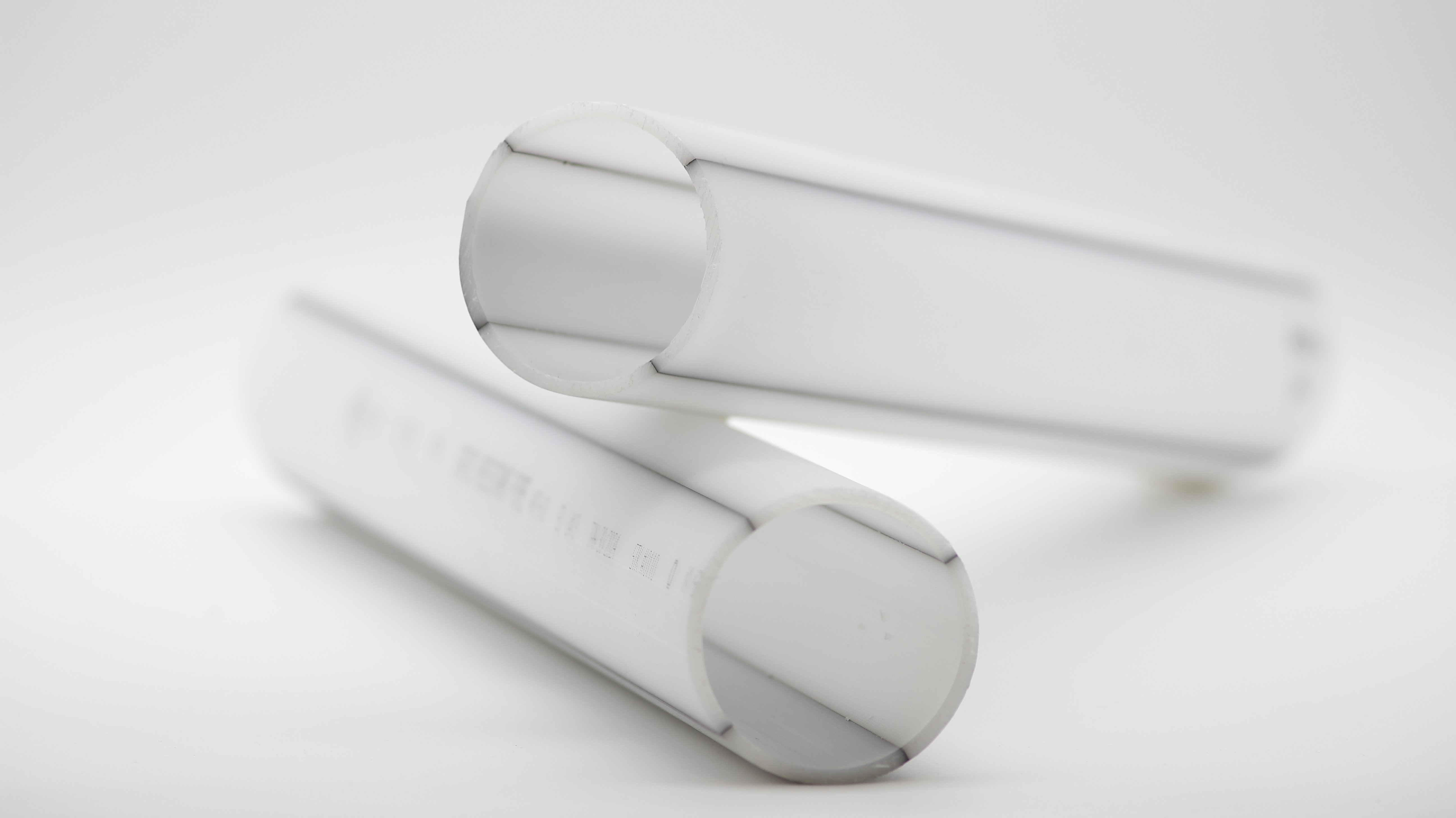
Graphmatech currently has a pilot-scale facility, and its long-term goal is to supply advanced materials rather than establish full-scale manufacturing of finalised components or systems.
Some companies may also choose to license the technology rather than source the material directly."
The company is currently undertaking trials with two packaging companies for applications requiring better barrier properties with fewer layers.. Another example of barrier application is hydrogen storage and transportation.
When storing hydrogen, leakage is a significant concern—not only from a cost perspective but also for safety and environmental reasons. Hydrogen is 11 times more harmful than carbon dioxide when released into the atmosphere, making containment critical.
Nestius explains:
“By incorporating graphene into the material, we reduce hydrogen leakage by up to 83 per cent, thanks to its exceptional barrier properties.
We currently have two packaging companies testing our materials, with an expected demand of 500 tonnes per year, which would significantly scale up our production.”
Additionally, for pipeline applications, there is an indicated requirement of 2-3 tonnes per month, totaling 25-35 tonnes per year.”
To meet these growing needs, Graphmatech is investing in a new machine that will increase its production capacity from just a few tonnes per year to 100–300 tonnes per year.
Lead image: Graphmatech.
Would you like to write the first comment?
Login to post comments